79 f350 crossover pittman arm???
#61
dana 44 crossover steering with a 1" spacer.
Not planning on heat treating them thats why i want to know what steel the longer studs are made of and then make mine stronger.The shoulder will be the same as original just 1" longer.
I know spacer sounds dodgy but the easiest way out.If welded to the arm would that help with strenght.
Do you know guys that run them successfully?
Not planning on heat treating them thats why i want to know what steel the longer studs are made of and then make mine stronger.The shoulder will be the same as original just 1" longer.
I know spacer sounds dodgy but the easiest way out.If welded to the arm would that help with strenght.
Do you know guys that run them successfully?
#62
If the shoulder of the stud is the same length as the shorter one, the stud cant provide enough surface area for the steering arm to make contact. This means that you will have a weak point. Thats what the shoulder is for. More contact area means more strength. Touch the surfaces with a threaded surface and both the stud and steerin arm will be comporomised and it will fail.
What material is this steering arm? IS it an aftermarket arm? Why is the drag link making contact with the spring pack? Has to be some circumstance that is making this an exceptional install.
Welding stuff together is probably not the solution since the problem is simnply being able to apply enough clamping force to maintian a reasonable amount of torque to the fasteners. Keep in mind that these arms are under a pretty severe load and this load is a side load and the studs are always in sheer.
Welding will undoubtedly warp the mating surfaces and the lack of flat surface will require that the studs do more work than necessary to clamp all of the parts together.
This is why we do not see arms powder coated or painted. The surfaces have to be as close to a perfect fit as possible with no deviations.
Have you any pics of your current set up?
What material is this steering arm? IS it an aftermarket arm? Why is the drag link making contact with the spring pack? Has to be some circumstance that is making this an exceptional install.
Welding stuff together is probably not the solution since the problem is simnply being able to apply enough clamping force to maintian a reasonable amount of torque to the fasteners. Keep in mind that these arms are under a pretty severe load and this load is a side load and the studs are always in sheer.
Welding will undoubtedly warp the mating surfaces and the lack of flat surface will require that the studs do more work than necessary to clamp all of the parts together.
This is why we do not see arms powder coated or painted. The surfaces have to be as close to a perfect fit as possible with no deviations.
Have you any pics of your current set up?
#63
I know the shoulder story that why it will be 1" longer will a 1" spacer.
The arm is 30mm mild steel .20mm rose joints,draglink is 8mm wall bar,which if bent would be a bit short and hard to bend..Axle moved forward aswell that the main problem why the drag is touching the springs.Touches alttle only at full lock.
How much will a 30mm piece of steel warp when welded.Wanted to put spacer, bolt the arm in then weld just to relieve the bolts abut almost as if it was one solid piece of steel.
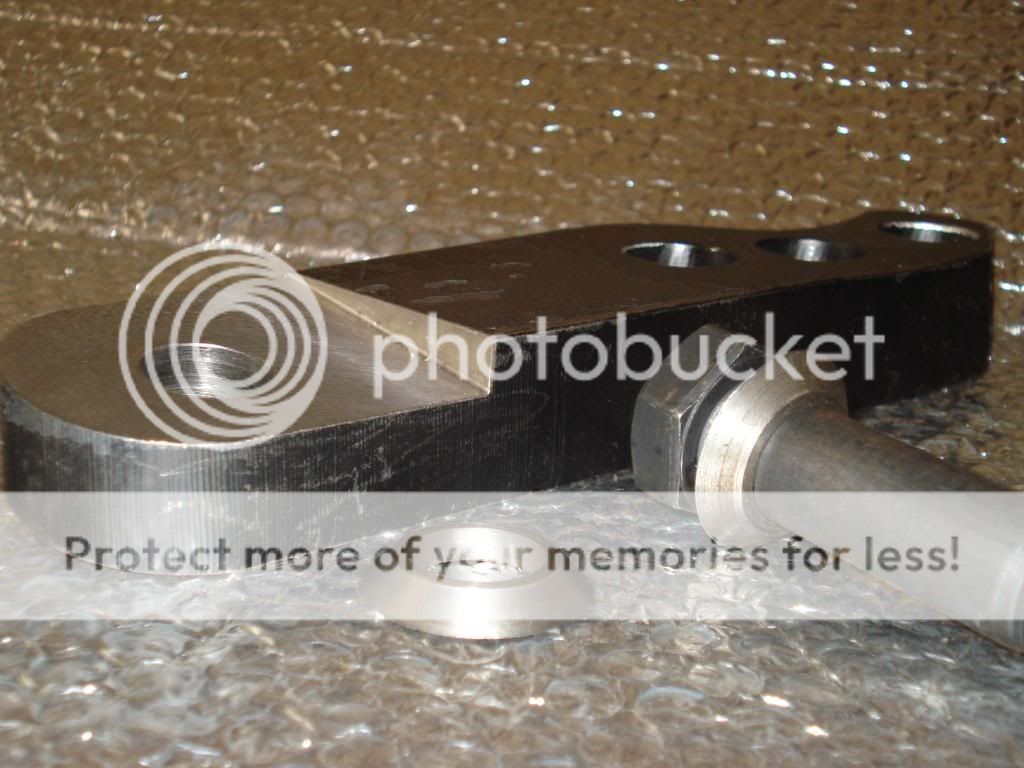
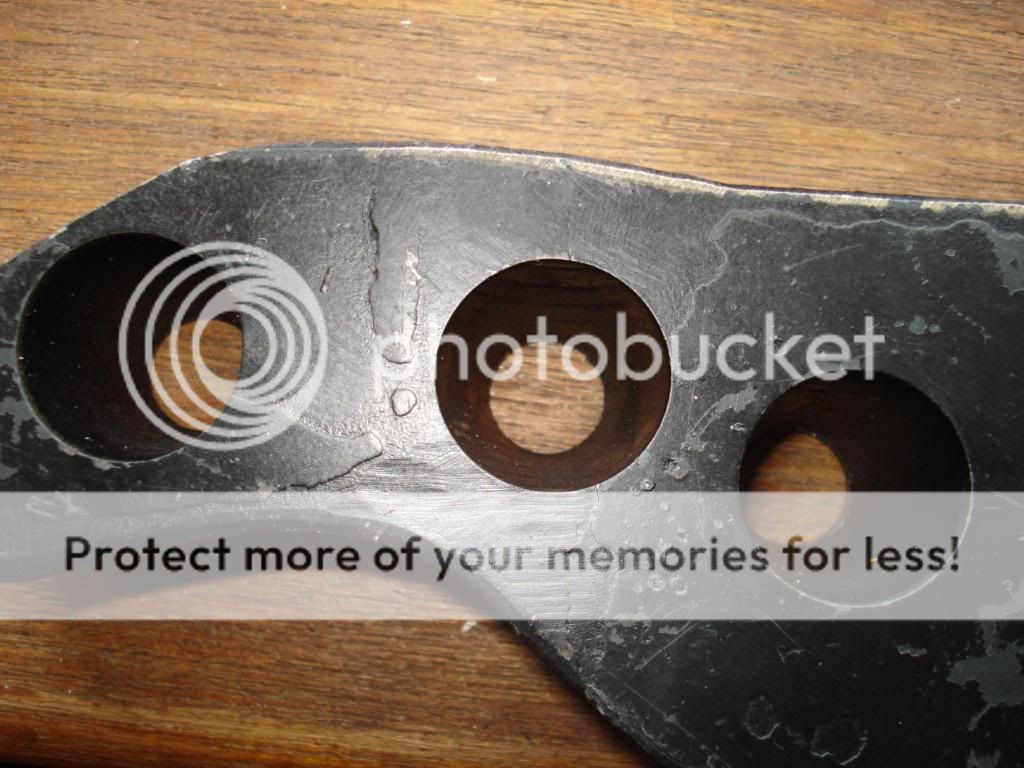
The arm is 30mm mild steel .20mm rose joints,draglink is 8mm wall bar,which if bent would be a bit short and hard to bend..Axle moved forward aswell that the main problem why the drag is touching the springs.Touches alttle only at full lock.
How much will a 30mm piece of steel warp when welded.Wanted to put spacer, bolt the arm in then weld just to relieve the bolts abut almost as if it was one solid piece of steel.
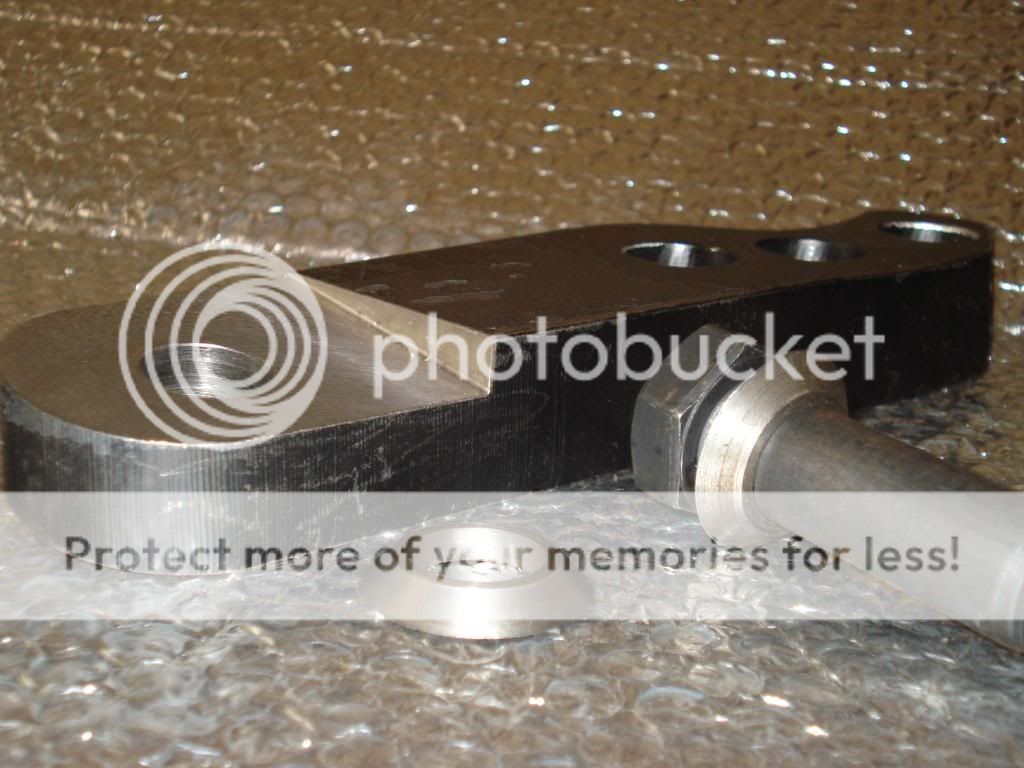
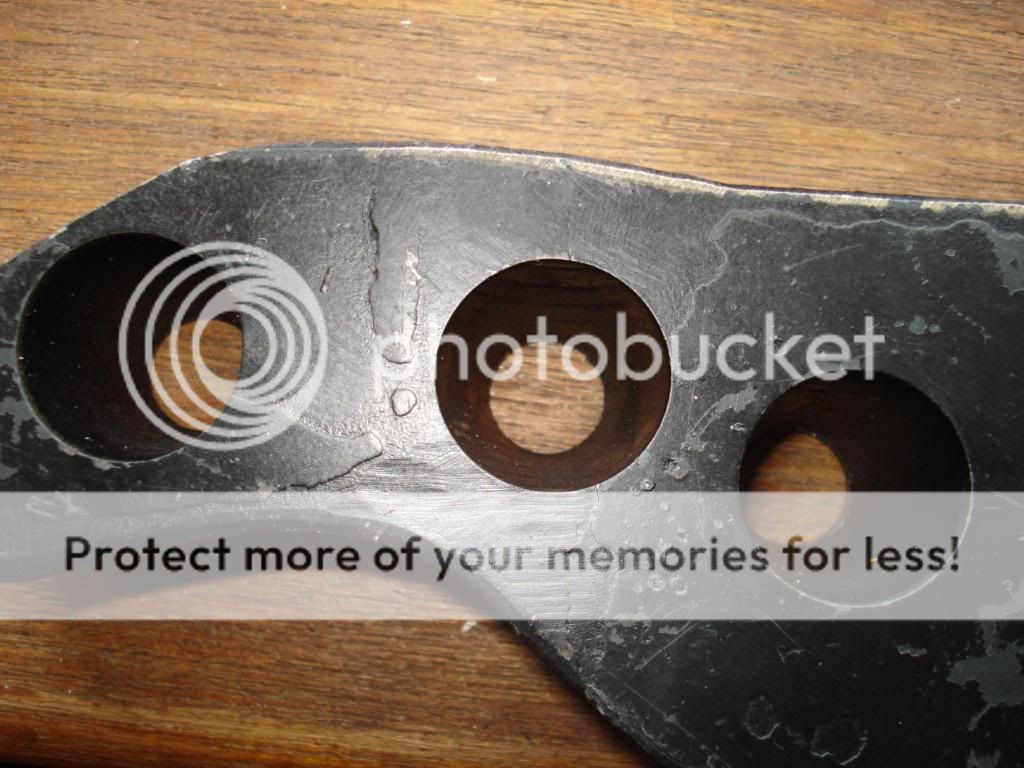
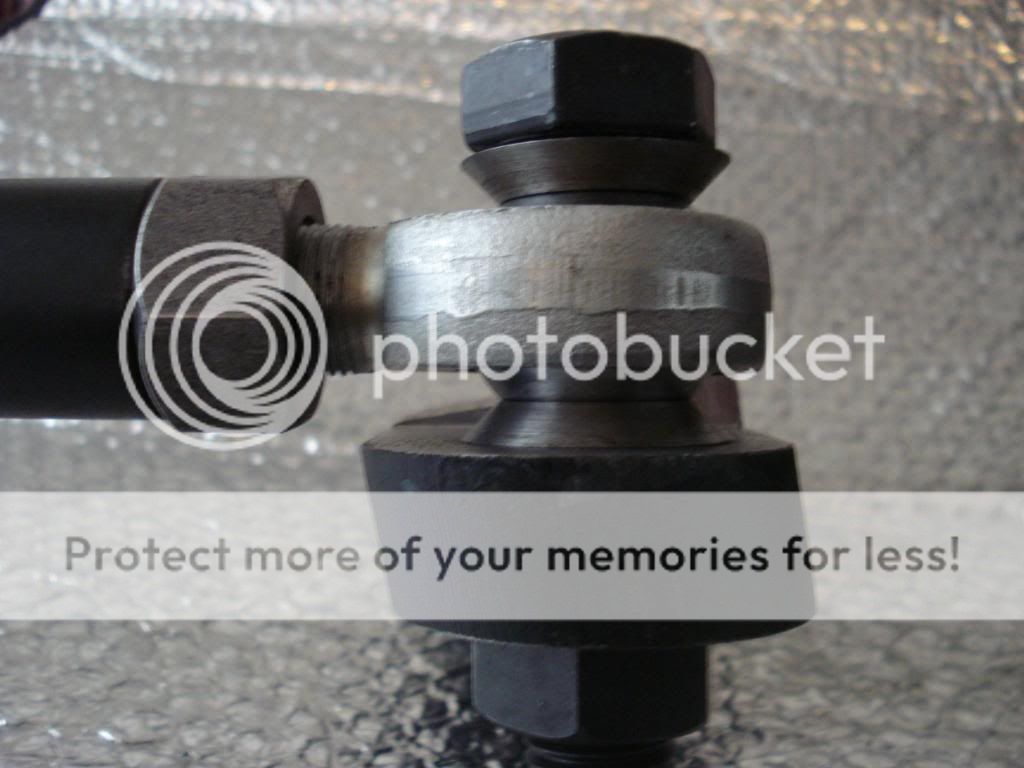
#64
You are more than welcome to weld if you wish. Any amount of heat will distort the machined surface.
Case in point:
I am currently re-building a Dana 60F and found some simple discrepancies with the short side tube. Made some aluminum slugs to simulate the carrier bearings so that I could pre-load the caps. Bored a hole through the center so that a long boring bar could fit through the entire axle. This was used to determine whether or not the axle housing was straight. It was not. Turned out that the previous owner welded some stuff to the tube and the heat generated by the welding pulled the tube almost .177" in one direction. This would have been enough to cause a leak in the inner seal.
Could this be tolerated? Perhaps. WOuld it have leaked for sure? Maybe, maybe not.
Is leaving it the absolute best way to solve the problem? Not in my eyes, but I am just one guy and opted to put it on a jig and straighten it. Simple approaches provide a much better long term solution.
In your case, instead of re-engineering the steering arm, you have a shperical rod end that is easiest to use a high mis-alignment bushing and a different bolt to attach it to the arm. This mis-alignment bushing will provide additional heigth and solve your clearance issues. Since you uare using a 3/4" bolt you should have no problems with the load. You may want to increase the sixe of that shperical rod end, and then use a strong 3/4" F911 bolt with the appropriate high mis-alignment bushing, and you dont have to get so creative with the arm Your studs will be fine and you dont have to worry anout it coming apart.
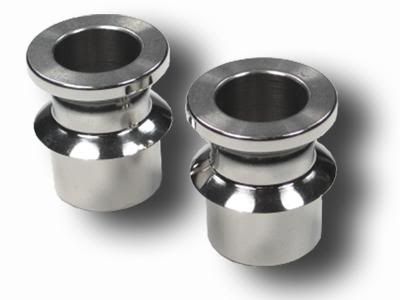
These insert into a larger rod end, and create a stronger joint or union when compared to the little spacer things that you have there.
These can be machined in Stainless or chro-mo. I use chro mo, but stainless is popular.
Notice the rise that one can expect from this set up. You may fint that this will solve your problem. YOu dont have to buy three studs or weld a spacer, just the right rod end and hardware. This is more reliable.
Case in point:
I am currently re-building a Dana 60F and found some simple discrepancies with the short side tube. Made some aluminum slugs to simulate the carrier bearings so that I could pre-load the caps. Bored a hole through the center so that a long boring bar could fit through the entire axle. This was used to determine whether or not the axle housing was straight. It was not. Turned out that the previous owner welded some stuff to the tube and the heat generated by the welding pulled the tube almost .177" in one direction. This would have been enough to cause a leak in the inner seal.
Could this be tolerated? Perhaps. WOuld it have leaked for sure? Maybe, maybe not.
Is leaving it the absolute best way to solve the problem? Not in my eyes, but I am just one guy and opted to put it on a jig and straighten it. Simple approaches provide a much better long term solution.
In your case, instead of re-engineering the steering arm, you have a shperical rod end that is easiest to use a high mis-alignment bushing and a different bolt to attach it to the arm. This mis-alignment bushing will provide additional heigth and solve your clearance issues. Since you uare using a 3/4" bolt you should have no problems with the load. You may want to increase the sixe of that shperical rod end, and then use a strong 3/4" F911 bolt with the appropriate high mis-alignment bushing, and you dont have to get so creative with the arm Your studs will be fine and you dont have to worry anout it coming apart.
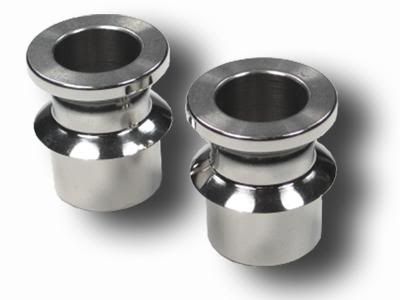
These insert into a larger rod end, and create a stronger joint or union when compared to the little spacer things that you have there.
These can be machined in Stainless or chro-mo. I use chro mo, but stainless is popular.
Notice the rise that one can expect from this set up. You may fint that this will solve your problem. YOu dont have to buy three studs or weld a spacer, just the right rod end and hardware. This is more reliable.
#65
yes good idea.I dont need the extra angle that these create.i know they give hight too.If i were to use bigger ends with the same bolt then the arm will need to be drilled even bigger/weaker.I have bolts that are maybe stronger than F911's and are press fitted in to pitman and steering arm ,zero movement.
Those were machined up and cost alot The shanked part is perfect and all spaced out for safety washers and all.So cant space up there.There must be plenty rigs running the spacer.Otherwise i must make a new arm but will still need the longer studs.Would grade 8 studs in your opinion be strong enough.Here they are called 10'8 also get 12.8.
Swopped in the HP 44 now so will see how it works with that.extra caster will also point the arm up a bit.
If the arm is bolted with the spacer tight then welded will the joined surface between the spacer and arm deform.The bottom(on knuckle) can always be skimmed again.If i weld slowly with little heat.
Those were machined up and cost alot The shanked part is perfect and all spaced out for safety washers and all.So cant space up there.There must be plenty rigs running the spacer.Otherwise i must make a new arm but will still need the longer studs.Would grade 8 studs in your opinion be strong enough.Here they are called 10'8 also get 12.8.
Swopped in the HP 44 now so will see how it works with that.extra caster will also point the arm up a bit.
If the arm is bolted with the spacer tight then welded will the joined surface between the spacer and arm deform.The bottom(on knuckle) can always be skimmed again.If i weld slowly with little heat.
#66
If you use the high mis-alignment bushings the hole for the arm is actually the same size. It will remain 3/4" even though you might be using a 7/8" or larger spherical rod end.
See the spacer is actually an insert. You insert the spacer into the top and bottom of the ball in the rod end. There is an OD and an ID of the spacer. The OD of the spacer is just under the ID of the rod end for a perfect fit. The bolt hole is reduced from say 7/8" to 3/4" so you will have the same sized bolt.
The 3/4" Grade-9 F911® 190,000 psi Bolts are stated as the strongest in it's class which is the reason they are used in the Aerospace industry. The 8640 alloy has 56% more Chromium & 100% more Nickel than other Grade-9 's. Bolt heads are 30% thicker. The smooth shoulder is also extended to provide maximum contact surface to the knuckle/rod end rather than against the threaded portion for a secure fit.
Have only seen one broken bolt ever. This was a vehicle involved in a crash that was insane.
Here is what the bushing looks like installed:
See the spacer is actually an insert. You insert the spacer into the top and bottom of the ball in the rod end. There is an OD and an ID of the spacer. The OD of the spacer is just under the ID of the rod end for a perfect fit. The bolt hole is reduced from say 7/8" to 3/4" so you will have the same sized bolt.
The 3/4" Grade-9 F911® 190,000 psi Bolts are stated as the strongest in it's class which is the reason they are used in the Aerospace industry. The 8640 alloy has 56% more Chromium & 100% more Nickel than other Grade-9 's. Bolt heads are 30% thicker. The smooth shoulder is also extended to provide maximum contact surface to the knuckle/rod end rather than against the threaded portion for a secure fit.
Have only seen one broken bolt ever. This was a vehicle involved in a crash that was insane.
Here is what the bushing looks like installed:
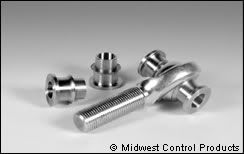
#67
Yes i wanted to keep the same size bolt and not go smaller.But 3/4 isnt that much smaller.How much higher can the spacers go ,can in get 1".
I understand that the spacer has better surface contact and a larger area ,how about doing the opposite instead of fitting inside the hole it fits on top of the end of arm both sides and end( all three sides) and then in top.With the bolt through it.Just an idea.
Then new longer bolt will be needed so will do misalignment route.
Thanks dude
I understand that the spacer has better surface contact and a larger area ,how about doing the opposite instead of fitting inside the hole it fits on top of the end of arm both sides and end( all three sides) and then in top.With the bolt through it.Just an idea.
Then new longer bolt will be needed so will do misalignment route.
Thanks dude
#68
Well I hope that the idea worls out for you. I believe this to be the safest and strongest route.
I think I recall a conversation not long ago. Your stuff is metric right? You had all of these things custom machined? Why was that again? Is there a reason why mail order stuff cant work for you?
I can send you some dimensions of the misalignment bushings and you can actually have some made. So far you have some serious machining being done, a set of spacers like this should be a piece of cake.
I also had another thought. Is the drag link close enough to the frame on the driver side to help your clearance problem? I mean if it is too low because the pitman arm is dropped too far, you will have a clearance problem on the pass side. Could this be a contributing factor?
I think I recall a conversation not long ago. Your stuff is metric right? You had all of these things custom machined? Why was that again? Is there a reason why mail order stuff cant work for you?
I can send you some dimensions of the misalignment bushings and you can actually have some made. So far you have some serious machining being done, a set of spacers like this should be a piece of cake.
I also had another thought. Is the drag link close enough to the frame on the driver side to help your clearance problem? I mean if it is too low because the pitman arm is dropped too far, you will have a clearance problem on the pass side. Could this be a contributing factor?
#70
Even though they are mass produced, they are produced by different machine shops for different suppliers. This means that there is not a set dimension other than the ID and OD of the bushing itself. The heigth can vary, and they do not have to be equal. IN other words one side does not have to be the same as the other, as long as the rod end does not bind when the link reaches a given angle. Spacers are also available and follow this principle.
Which box did you use? Does the pitman arm sit as close to the frame as possible?
Have you cycled the suspension to verify clearance during full suspension extension as well as compression?
Follow this link:
http://www.midwestcontrol.com/catdis...ort.php?pg=228
There are dimensional sketches as well as CAD dwgs that you may find usefull. YOu may also purchase or have your machinist copy and even modify these to accomodate your specific requirements.
I thought of something last night? Is the reason why your drag link is hitting the spring because you are using a very thick spring pack? Could it be that caster is such that the axle is rolled to far forward? Since the steering arm is attached directly to the knuckle, it is possible to experience your problem if the caster is too negative (too far forward).
This will lower the end of the steering arm thus limiting the clearance between the end of the steering arm and the spring pack.
Combine the two symptoms and you will have to get real creative to fix the hidden issues.
Some greater issue might be in play here, and we may be over thinking this whole thing when a simple solution might be what we should be looking at.
Do you have any pics of this stuff installed? Box, drag link, steering arm etc?
Which box did you use? Does the pitman arm sit as close to the frame as possible?
Have you cycled the suspension to verify clearance during full suspension extension as well as compression?
Follow this link:
http://www.midwestcontrol.com/catdis...ort.php?pg=228
There are dimensional sketches as well as CAD dwgs that you may find usefull. YOu may also purchase or have your machinist copy and even modify these to accomodate your specific requirements.
I thought of something last night? Is the reason why your drag link is hitting the spring because you are using a very thick spring pack? Could it be that caster is such that the axle is rolled to far forward? Since the steering arm is attached directly to the knuckle, it is possible to experience your problem if the caster is too negative (too far forward).
This will lower the end of the steering arm thus limiting the clearance between the end of the steering arm and the spring pack.
Combine the two symptoms and you will have to get real creative to fix the hidden issues.
Some greater issue might be in play here, and we may be over thinking this whole thing when a simple solution might be what we should be looking at.
Do you have any pics of this stuff installed? Box, drag link, steering arm etc?
#71
No pics intalled.
Caster i have about 5' now which is fine i think.Thought of that but would have to make the caster greater to help.Only have 4 blades now pulled two.
How much lift do you have and how much space have you got above your betweeb drag and springs.
I have a zf power box with the 3 mounting holes.
Caster i have about 5' now which is fine i think.Thought of that but would have to make the caster greater to help.Only have 4 blades now pulled two.
How much lift do you have and how much space have you got above your betweeb drag and springs.
I have a zf power box with the 3 mounting holes.
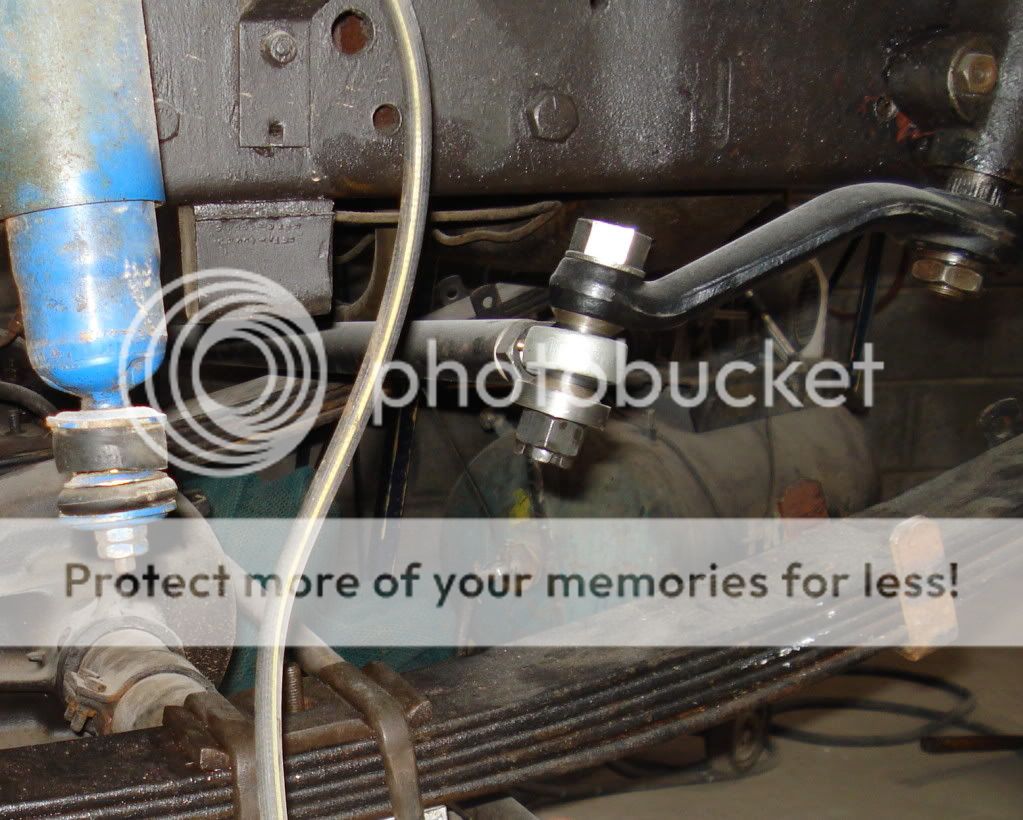
#73
I have morel ift than you do, but I have more leafs in my spring pack as well, almost twice the amount of leafs pictured above.
I run a D 60 up front so my knuckle is larger and this additional heigth might make this an apples to oranges comparisson.
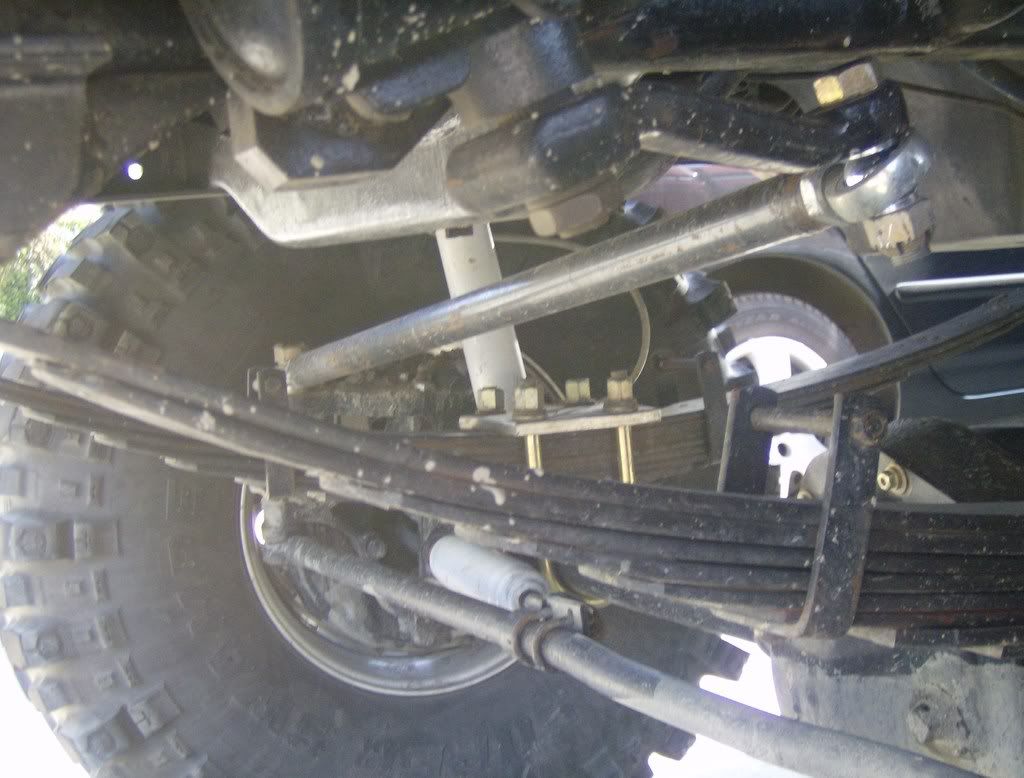
I dont have much clearance between my spring and the drag link. Since the knuckle and drag link move exactly the same, there is never any trouble with clearance. The steering box side is another story. I run this side as tight to the frame as possible. I still hit the pitman arm with the spring when compression gets crazy sick.
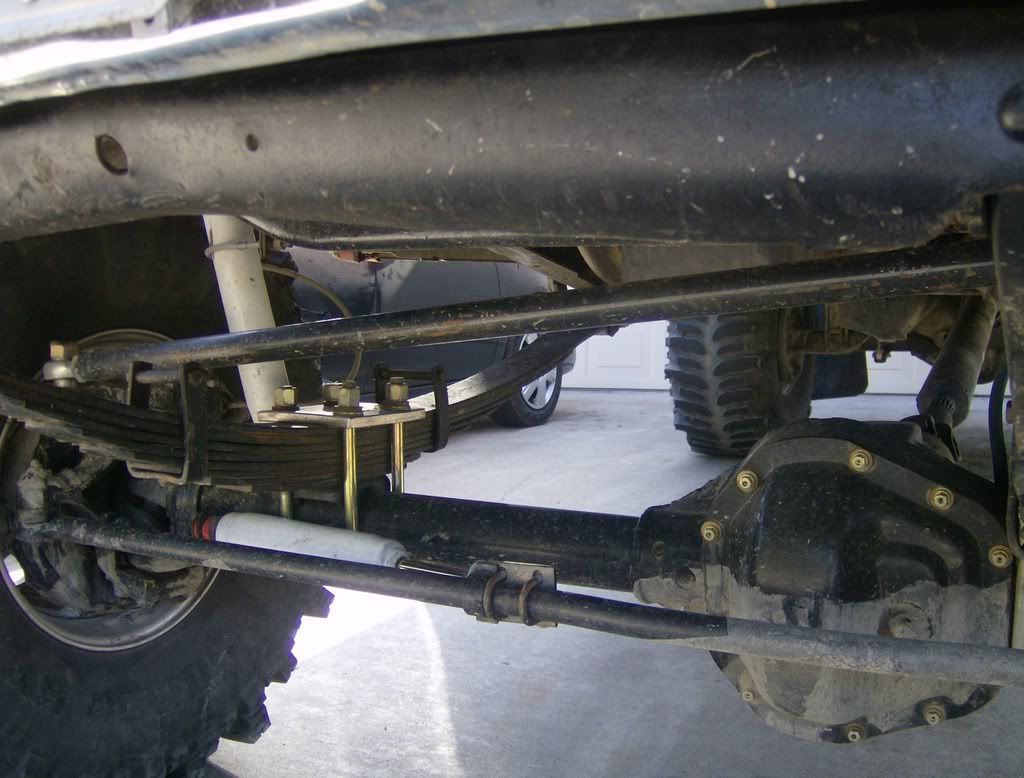
Pinion angle in minimal. This was from many moons ago, but it is the best shot of the angle that I have. I keep the angle to a minimum, and the pinion points right at the tcase. Not an up angle and not down like the low pinion. This permits the widest amount of movement without binding when the suspension cycles.
I have run both, doubles and singal cardans with the same angles. The 1350 double cardan has an advantage under extreme suspension extension but the larger 1410 single joints can work at greater angles, so this boils down to which joint can work at a given angle and how much your suspension can cycle.
With the very long front driveshaft, the driveline angle is seldom a problem. Caster is more critical than anything.
I run a D 60 up front so my knuckle is larger and this additional heigth might make this an apples to oranges comparisson.
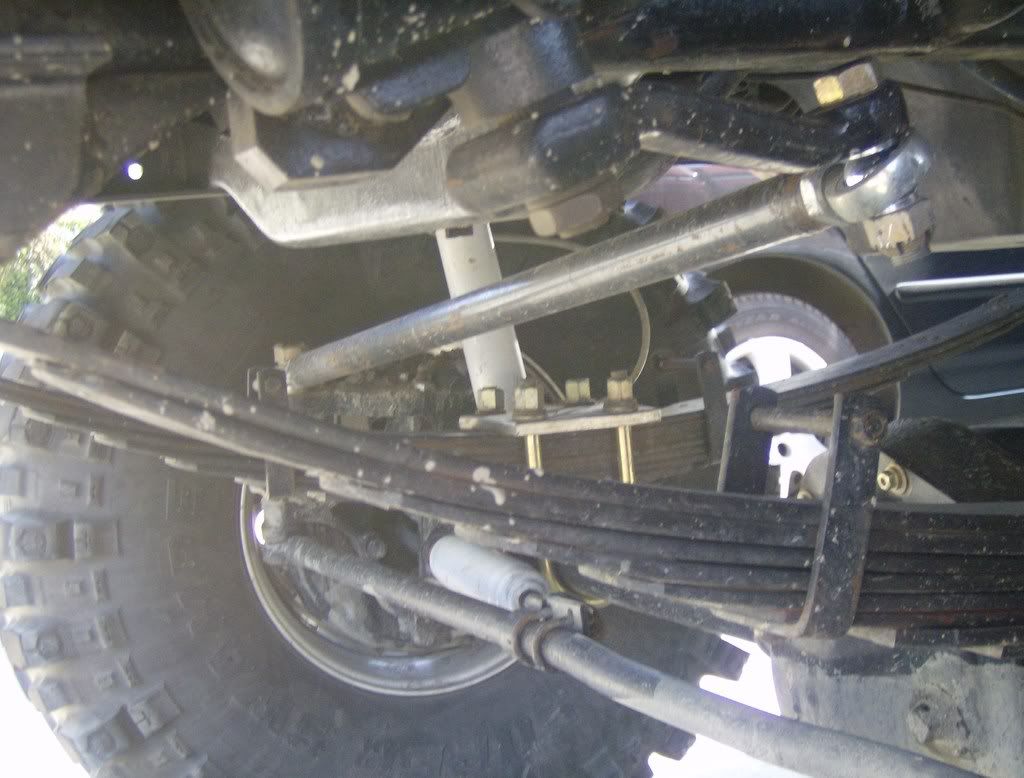
I dont have much clearance between my spring and the drag link. Since the knuckle and drag link move exactly the same, there is never any trouble with clearance. The steering box side is another story. I run this side as tight to the frame as possible. I still hit the pitman arm with the spring when compression gets crazy sick.
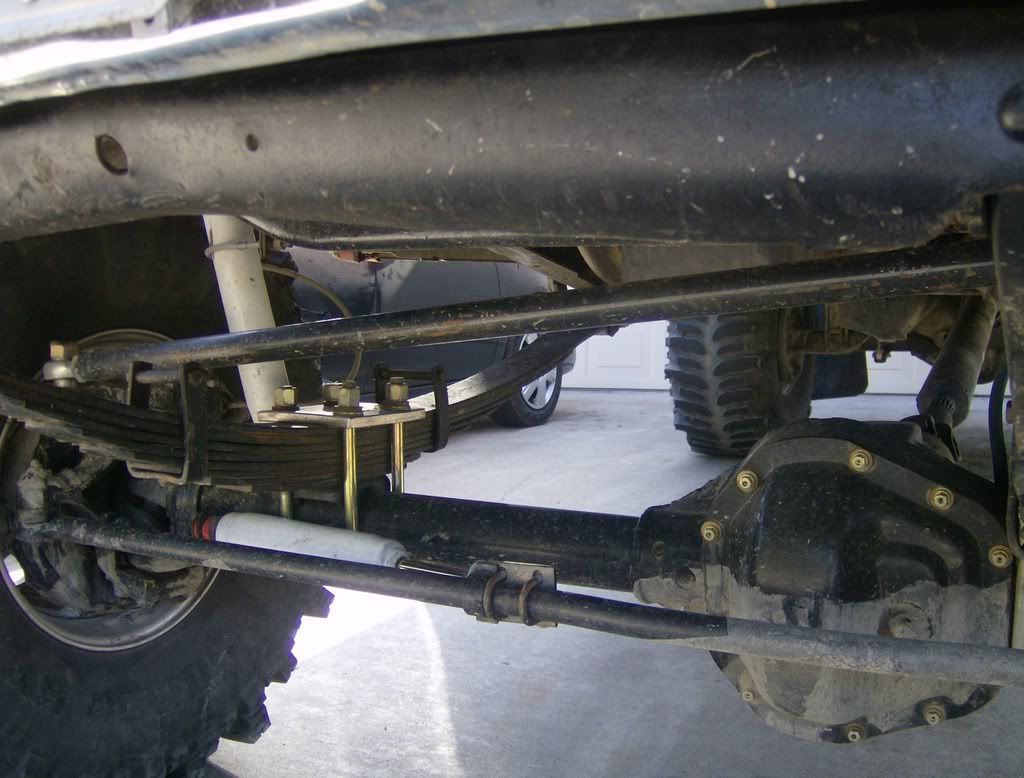
Pinion angle in minimal. This was from many moons ago, but it is the best shot of the angle that I have. I keep the angle to a minimum, and the pinion points right at the tcase. Not an up angle and not down like the low pinion. This permits the widest amount of movement without binding when the suspension cycles.
I have run both, doubles and singal cardans with the same angles. The 1350 double cardan has an advantage under extreme suspension extension but the larger 1410 single joints can work at greater angles, so this boils down to which joint can work at a given angle and how much your suspension can cycle.
With the very long front driveshaft, the driveline angle is seldom a problem. Caster is more critical than anything.

#74
Thats helps alot thanks.
Just thought know when the guy just general engineer nilled my old knuckle he milled it level taking the angle away so it is not pointing up as it could have.
The HP should actually work then.The 60 is alot higher on the knuckle.
So the long shaft with divorced case wont give noticeable vibration if case is 5" up and so is pinion ?
DO you think safety washers are important?And i have a washer under heim bolt head and by nut and safety washer you dont,neither do TRE's is it better not to have them?
CHEERS
Just thought know when the guy just general engineer nilled my old knuckle he milled it level taking the angle away so it is not pointing up as it could have.
The HP should actually work then.The 60 is alot higher on the knuckle.
So the long shaft with divorced case wont give noticeable vibration if case is 5" up and so is pinion ?
DO you think safety washers are important?And i have a washer under heim bolt head and by nut and safety washer you dont,neither do TRE's is it better not to have them?
CHEERS
#75
Thats helps alot thanks.
Just thought know when the guy just general engineer nilled my old knuckle he milled it level taking the angle away so it is not pointing up as it could have.
The HP should actually work then.The 60 is alot higher on the knuckle.
So the long shaft with divorced case wont give noticeable vibration if case is 5" up and so is pinion ?
DO you think safety washers are important?And i have a washer under heim bolt head and by nut and safety washer you dont,neither do TRE's is it better not to have them?
CHEERS
Just thought know when the guy just general engineer nilled my old knuckle he milled it level taking the angle away so it is not pointing up as it could have.
The HP should actually work then.The 60 is alot higher on the knuckle.
So the long shaft with divorced case wont give noticeable vibration if case is 5" up and so is pinion ?
DO you think safety washers are important?And i have a washer under heim bolt head and by nut and safety washer you dont,neither do TRE's is it better not to have them?
CHEERS
It is much better to have them. My rigs are maintenance machines. They come apart all of the time, and I replace spherical rod ends after a given season. If I impact a component, it gets replaced.
This set up has since changed and I do run a saftey washer. If you have them use them just make sure that it does not bind the rod end or it will promote problems and stress the ball to the point where the saftey device might actually cause the rod end to pop off.
This is where cycling the suspension become critical.