I'm thinking of installing a high-amp DC plug near my receiver hitch
#16
We never rely on the chassis for a ground.
Depending on the cost at the time, either welding cable or marine grade Ancor battery cable. Most recently our best cost for 4/0 was amazon.
Typical for us is 2/0 welding cable with Anderson connectors. We have Anderson connectors on everything 12 volts.
Positive on the dual battery trucks comes right of the starter.
Negative is run to the ground connection on the engine block.
Even using the chassis you still have to calculate the run. Numbers change, but the length is still added.
We use the 175 connector on everything. Even items only needing 15-20 amps get the big connector. Keeps everything uniform.
Circuit protection should be at the source.
Circuit protection protects the wire, not the appliance or source.
#17
I am not an electrician, but my understanding is that all power sources need to be provided overcurrent protection. The remote battery that you are directly feeding (charging) with permanently attached heavy gauge cables is also a power source. When the tow vehicle is shut off or disconnected from the remote battery, the remote battery is now its own power source that is energizing that same heavy gauge positive charge wire all the way back to the point of disconnection/connection at the front of the trailer/vehicle. If something happens to that section of positive wire (someone cuts into or it chafes to ground, etc) it will create a direct battery short to ground. The MRCB breakers with manual trip/reset lever all also great because they serve as a simple and convenient means of manual disconnection/isolation for the remote battery in case you need to work on the heavy gauge circuit, or do not want somebody connecting to it and pulling the battery down (using your remote battery as their temporary power source).
#18
#19
We have been running heavy gauge cables to the rear of trucks for boats, trailers, winches, inverters, jumpers etc for years.
We never rely on the chassis for a ground.
Depending on the cost at the time, either welding cable or marine grade Ancor battery cable. Most recently our best cost for 4/0 was amazon.
Typical for us is 2/0 welding cable with Anderson connectors. We have Anderson connectors on everything 12 volts.
Positive on the dual battery trucks comes right of the starter.
Negative is run to the ground connection on the engine block.
Yes there is an electrical reason to using the vehicle chassis as a ground. Here's an example: You require an electrical outlet (Anderson plug, say) at the rear of your vehicle to power a device that draws 50 amps & the length of cable required to reach the plug is 7 metres. Now to calculate the cable size you have to take in the length of the return (negative) cable as well. Using the example requirements above with a twin cable installation i.e. positive & negative cables run to the plug from the battery & based on a battery voltage of 13.8 & a voltage drop of ~3% giving a working voltage of ~13.4 volts at the plug. You would need to run 14 metres of 4/0 AWG (B&S) cable. Whereas using the vehicle Chassis as the ground you would only have to run a 7m length of 5 AWG (B&S) plus a short length from the negative terminal of the plug to the chassis, say ~1 metre, bringing the total length to 8 metres of 5 AWG as against 14 metres of 4/0 AWG, a huge saving. A good idea is to upgrade the body & chassis ground cables from the negative terminal of the battery as the original cables are sized to the standard electrical load of the vehicle & may not be heavy enough to handle an increased load on the chassis ground.
Even using the chassis you still have to calculate the run. Numbers change, but the length is still added.
We use the 175 connector on everything. Even items only needing 15-20 amps get the big connector. Keeps everything uniform.
Why?
Circuit protection should be at the source.
Circuit protection protects the wire, not the appliance or source.
We never rely on the chassis for a ground.
Depending on the cost at the time, either welding cable or marine grade Ancor battery cable. Most recently our best cost for 4/0 was amazon.
Typical for us is 2/0 welding cable with Anderson connectors. We have Anderson connectors on everything 12 volts.
Positive on the dual battery trucks comes right of the starter.
Negative is run to the ground connection on the engine block.
Yes there is an electrical reason to using the vehicle chassis as a ground. Here's an example: You require an electrical outlet (Anderson plug, say) at the rear of your vehicle to power a device that draws 50 amps & the length of cable required to reach the plug is 7 metres. Now to calculate the cable size you have to take in the length of the return (negative) cable as well. Using the example requirements above with a twin cable installation i.e. positive & negative cables run to the plug from the battery & based on a battery voltage of 13.8 & a voltage drop of ~3% giving a working voltage of ~13.4 volts at the plug. You would need to run 14 metres of 4/0 AWG (B&S) cable. Whereas using the vehicle Chassis as the ground you would only have to run a 7m length of 5 AWG (B&S) plus a short length from the negative terminal of the plug to the chassis, say ~1 metre, bringing the total length to 8 metres of 5 AWG as against 14 metres of 4/0 AWG, a huge saving. A good idea is to upgrade the body & chassis ground cables from the negative terminal of the battery as the original cables are sized to the standard electrical load of the vehicle & may not be heavy enough to handle an increased load on the chassis ground.
Even using the chassis you still have to calculate the run. Numbers change, but the length is still added.
We use the 175 connector on everything. Even items only needing 15-20 amps get the big connector. Keeps everything uniform.
Why?
Circuit protection should be at the source.
Circuit protection protects the wire, not the appliance or source.
#20
#22
For anyone following, the isolator above won't work. I called the manufacturer and they said our HD alternators are too much for it.
Instead I opted for this: https://www.etrailer.com/p-331-BCDC1240D.html
My 2AWC wire is probably overkill, but will put me within the 3% critical voltage drop range. Actual drop assuming 14.08 (I measured it) at the battery:
Voltage drop: 0.38
Voltage drop percentage: 2.66%
Voltage at the end: 13.7
This unit will allow me to keep the trailer battery FULL despite running the residential fridge, and also isolate the starting batteries to avoid being stranded.
Additionally, when I upgrade my batteries, it will charge them correctly.
Finally, it also allows solar input and prioritizes it over your truck, so when I upgrade to solar on the top of the rig everything will be automatic.
Instead I opted for this: https://www.etrailer.com/p-331-BCDC1240D.html
My 2AWC wire is probably overkill, but will put me within the 3% critical voltage drop range. Actual drop assuming 14.08 (I measured it) at the battery:
Voltage drop: 0.38
Voltage drop percentage: 2.66%
Voltage at the end: 13.7
This unit will allow me to keep the trailer battery FULL despite running the residential fridge, and also isolate the starting batteries to avoid being stranded.
Additionally, when I upgrade my batteries, it will charge them correctly.
Finally, it also allows solar input and prioritizes it over your truck, so when I upgrade to solar on the top of the rig everything will be automatic.
#23
no problem. This is what I used. Quality item. Trombetta?s Bear DC Contactor, With 225 Amps Continuous Duty and 300 Amps Intermittent Duty Current Carrying Capability, Provides an Economical Solution to High Current Switching Applications
The biggest challenge you will have is finding a place to mount the breaker and contactor under the hood of the truck. I ended up mounting both on the front lower side of the firewall on the passenger side of the truck. Both are basically behind the inner fender liner (I have a 2016 F350). If you are lying on the ground behind the passenger side front tire, look up at the space between the firewall and the back side of the inner fender liner. Thats where I mounted both items. I can reach up with a 6” flat blade screw driver and trip or reset the breaker if needed. I coukd not find anywhere to mount both items from the top side of the engine compartment.
Can you detail the procedure for mounting the circuit breaker and contactor where you describe above? For a complete idiot about this stuff for me please?
For example...
1. I'm assuming I have to remove the fender liners (it appears there are two). Is this just the self tapping screws that line the outside of it? Anything to be aware of in that R&R procedure?
2. How high up in there did you mount the two components? I'm concerned about water intrusion so I'm assuming you got them high? If not, have you had any trouble with water?
3. Did you have to jack the truck up to do it? Take the wheel off?
4. Anything else I should be aware of?
#24
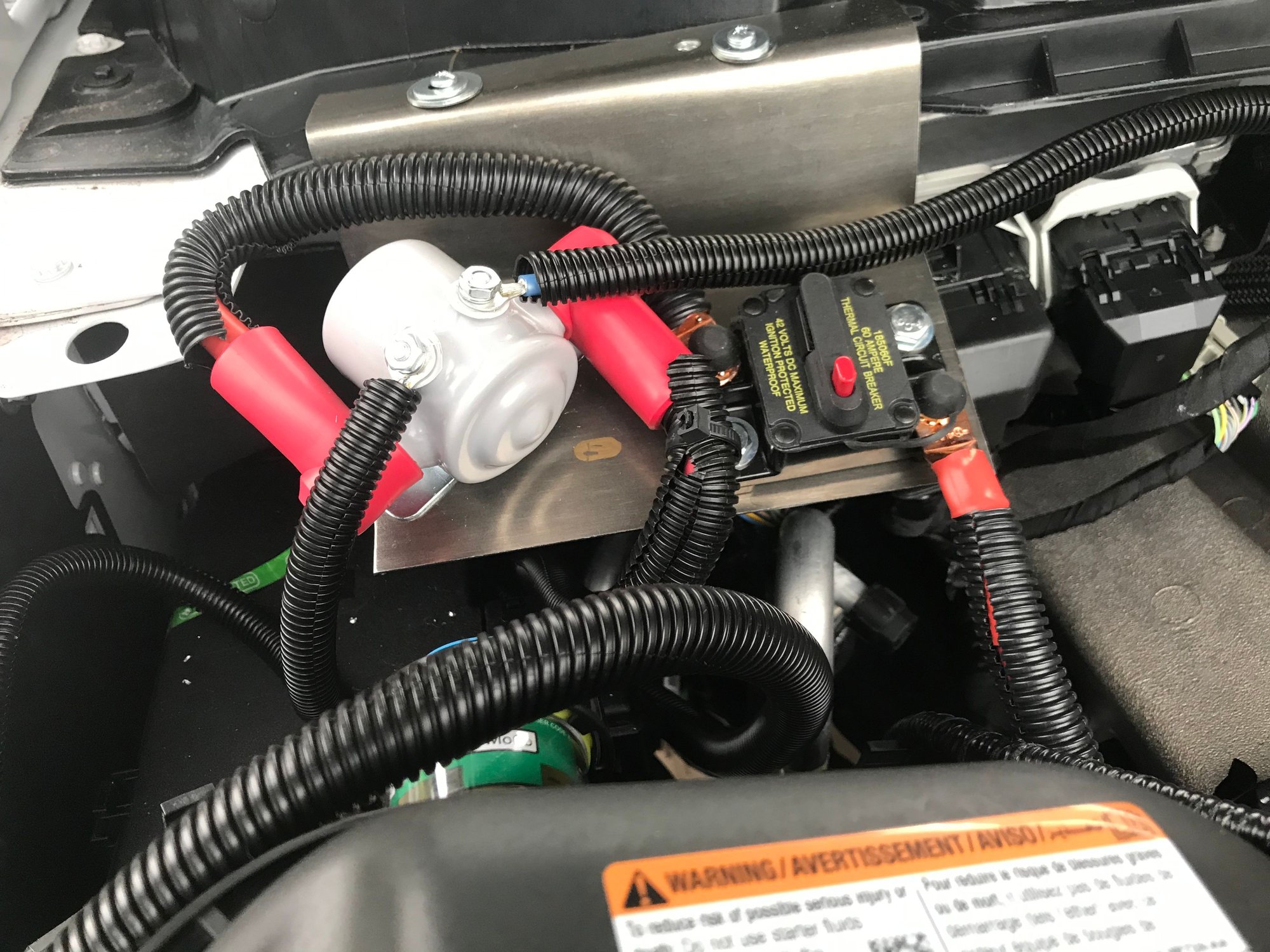

Well, I did it!
I made a lot lot of mistakes. Too many to count.
Some of of my favorites were dropping a wrench on top of the fender liner after I got it back on...so it had to come back off again. Or that one time, “at band camp,” when I stuck the positive wire into the Anderson connector and it didn’t fit. But my all time favorite has to be when I over tightened the shelf and broke the head off the screw.
There were some moments where I almost threw up... like when I drilled two, 3/4 inch holes through the bed, and when I saw metal while drilling through plastic for the shelf. Oh yeah...damaging the high amp upfitter insulation (both) while cutting off the zip tie.
But boy oh boy do I have an AMAZING charging system.
The solenoid is wired to switch #1, and I now have 14.74 volts direct from the battery via #2 wire all the way back near the tailgate inside the bed!
Thanks to all who helped in this thread and a couple others, with special thanks to skanj0 for above and beyond details and patience.
#27
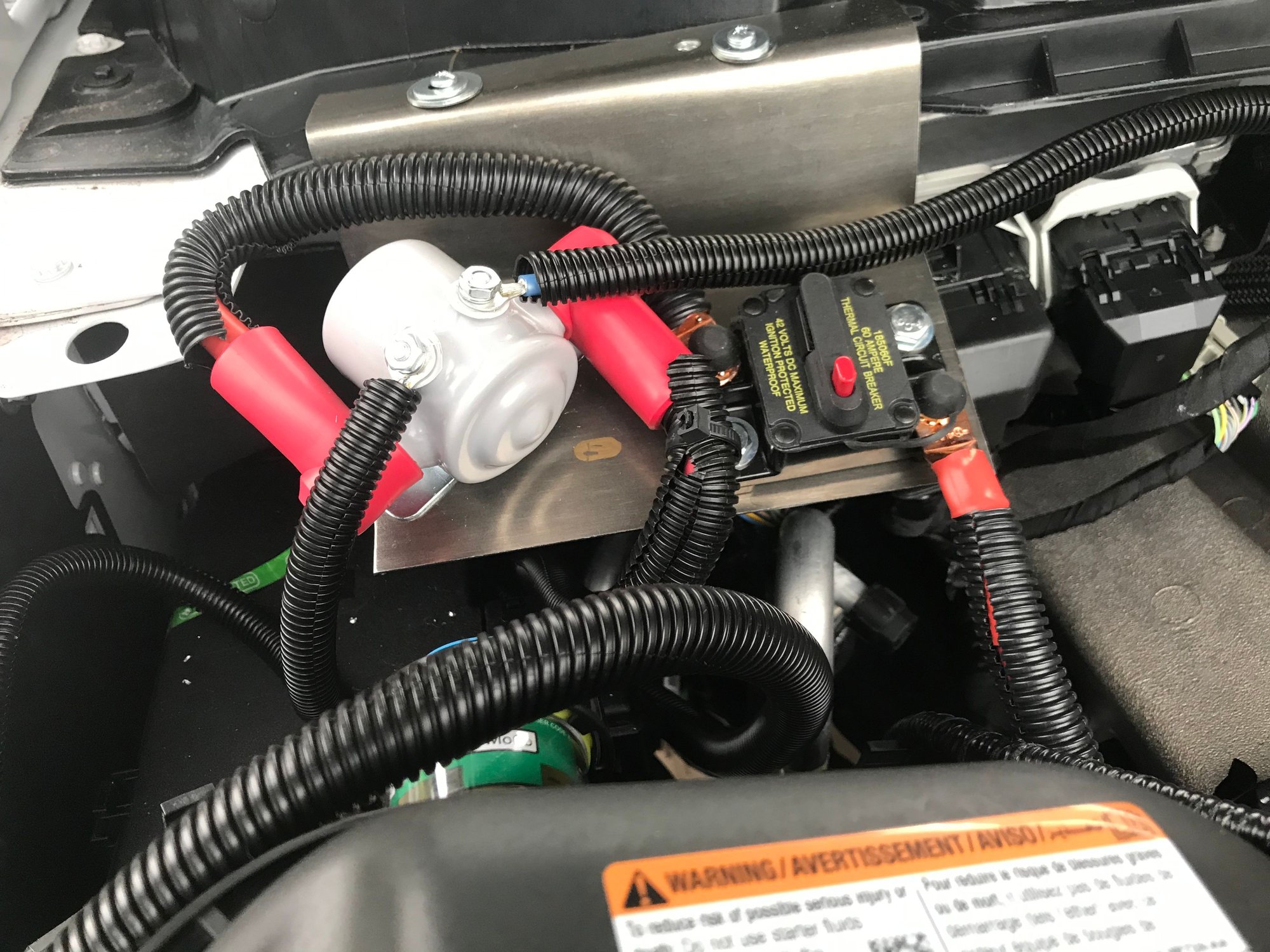

Well, I did it!
I made a lot lot of mistakes. Too many to count.
Some of of my favorites were dropping a wrench on top of the fender liner after I got it back on...so it had to come back off again. Or that one time, “at band camp,” when I stuck the positive wire into the Anderson connector and it didn’t fit. But my all time favorite has to be when I over tightened the shelf and broke the head off the screw.
There were some moments where I almost threw up... like when I drilled two, 3/4 inch holes through the bed, and when I saw metal while drilling through plastic for the shelf. Oh yeah...damaging the high amp upfitter insulation (both) while cutting off the zip tie.
But boy oh boy do I have an AMAZING charging system.
The solenoid is wired to switch #1, and I now have 14.74 volts direct from the battery via #2 wire all the way back near the tailgate inside the bed!
Thanks to all who helped in this thread and a couple others, with special thanks to skanj0 for above and beyond details and patience.
Great to hear you got it done. Sounds like it came out great.
Now for the trailer side!

#29
This is project pushed my comfort zone, but the good people here (and YouTube videos for how to crimp/solder/heat shrink made it go pretty well overall.